Unleashing Success in the Business of Mold Manufacturing within the Metal Fabrication Industry
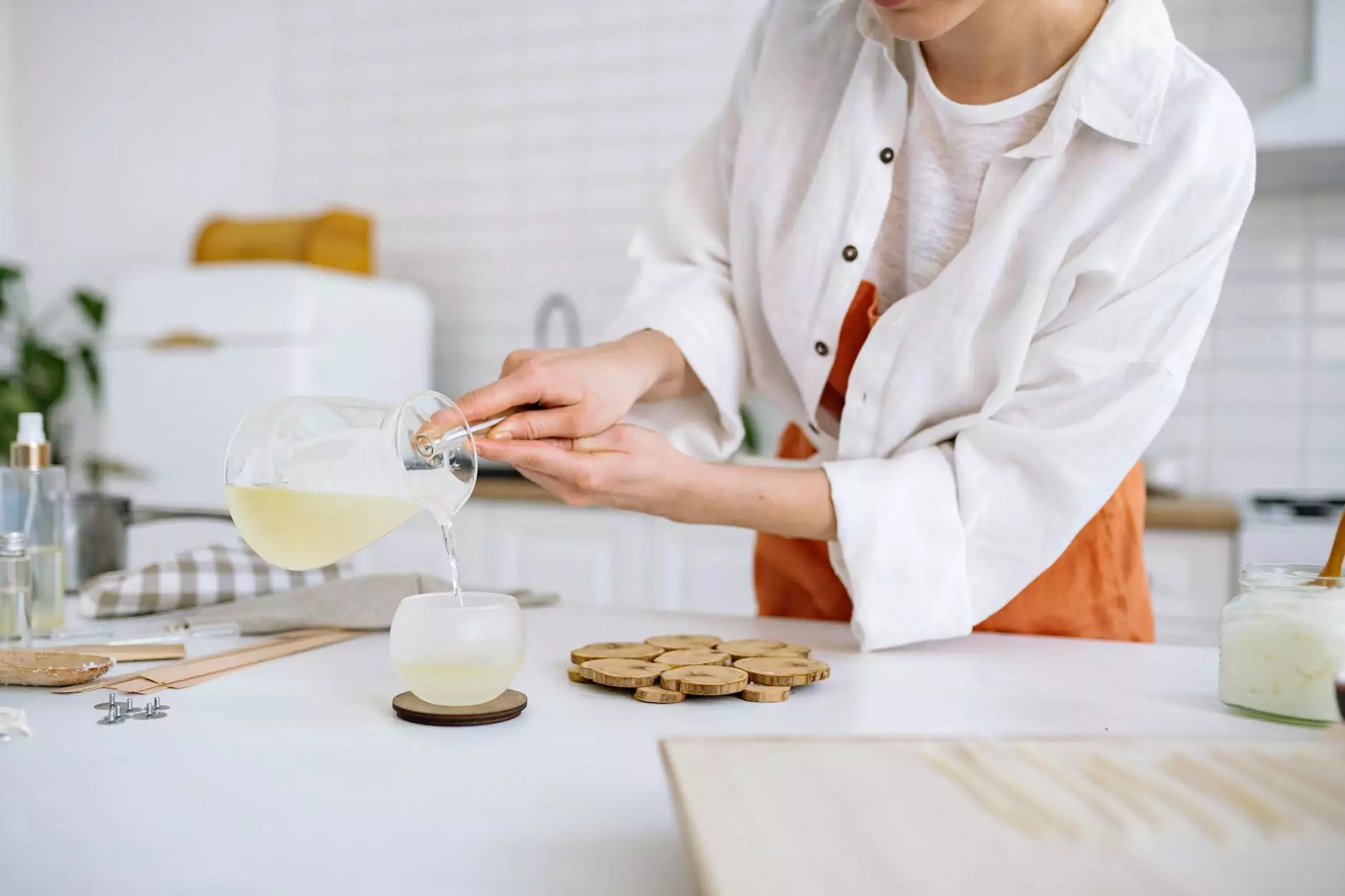
Themold manufacturer industry represents a cornerstone of the modern manufacturing landscape, integrating cutting-edge technology, skilled craftsmanship, and innovative business strategies to deliver high-precision molds for diverse sectors. As a critical element within the broader metal fabricators domain, successful mold manufacturing businesses are continually evolving to meet demanding industry standards, technological advancements, and customer expectations.
Understanding the Core of Mold Manufacturing in the Metal Fabrication Sector
At its essence, mold manufacturing entails designing and producing customized molds that serve as essential tools for shaping metal, plastics, and other materials in mass production processes. As an integral part of metal fabricators, mold manufacturers must blend artistry with technical finesse to produce durable, precise, and efficient molds that satisfy industry-critical standards.
Effective business strategies in this niche focus on multiple facets, including innovation, quality assurance, customer collaboration, and technological integration, all aimed at creating competitive advantages and fostering sustained growth.
The Growing Importance of Innovation in the Mold Manufacturer Business
Innovation is the heartbeat of successful mold manufacturers. From adopting advanced manufacturing technologies such as computer numerical control (CNC) machining, 3D printing, and additive manufacturing, to implementing sophisticated CAD/CAM software, cutting-edge tools empower mold companies to deliver high-precision molds efficiently and cost-effectively.
In today’s competitive marketplace, innovation also extends to material selection—embracing specialized alloys, high-performance steels, and advanced composites to enhance mold longevity and performance. Forward-thinking mold manufacturers are also investing in automation and smart factory solutions to streamline production and reduce errors, ultimately enhancing their value proposition to clients.
Key Business Opportunities for Mold Manufacturers in the Metal Fabrication Industry
- Automotive Industry: High-volume demand for durable, precise molds for parts such as engine components, interior fixtures, and exterior panels.
- Electronics and Consumer Goods: Requirement for intricate molds for plastic casings, connectors, and electronic device enclosures.
- Medical Devices: Production of highly accurate molds for medical instruments and packaging, emphasizing sterilization and biocompatible materials.
- Aerospace Sector: Precision molds capable of manufacturing complex aerospace components with stringent safety and quality standards.
- Packaging Industry: Creation of molds for containers, bottles, and packaging plastics that demand high efficiency and aesthetic appeal.
Each of these sectors presents lucrative opportunities for mold manufacturers willing to adapt to industry trends and leverage technological innovations.
Strategic Business Planning for a Mold Manufacturer
Building a resilient and profitable business in the mold manufacturer space requires meticulous planning and execution. Here are essential strategies:
1. Focus on Quality Assurance and Certifications
Quality is non-negotiable. Acquiring industry-standard certifications like ISO 9001 demonstrates commitment to excellence and enhances credibility among clients. Implementing rigorous testing procedures, maintaining strict tolerances, and employing high-grade materials ensure the durability and performance of molds, leading to satisfied customers and repeat business.
2. Invest in Cutting-Edge Technology
Maintaining competitiveness means constantly upgrading equipment and software. Investing in high-speed CNC machines, EDM (Electrical Discharge Machining), and 5-axis machining centers are vital for achieving complex geometries and tight tolerances. Additionally, harnessing CAD/CAM integration enables rapid prototyping, iterative design improvements, and faster turnaround times.
3. Foster Strong Client Relationships and Collaboration
Success in the mold manufacturing industry heavily relies on understanding client needs thoroughly. Effective communication, collaborative design processes, and transparent project management build client trust and lead to tailored solutions that meet specific industry requirements.
4. Emphasize Research and Development
Continuous R&D investment helps companies stay ahead of market trends, discover innovative mold materials, and develop new manufacturing processes. R&D initiatives also enable the production of more complex, multifunctional molds that give clients competitive advantages.
5. Expand Capacity and Scalability
Scaling production capabilities, whether through adding new machinery or expanding facilities, allows businesses to handle larger orders and diversify their product offerings. Scalability also involves establishing strategic partnerships with raw material suppliers and distribution channels.
Technological Trends Reshaping the Mold Manufacturer Business
The industry is undergoing a technological revolution that provides new avenues for efficiency, quality, and innovation:
- Artificial Intelligence (AI) and Machine Learning: Automate quality control, predict maintenance needs, and optimize design parameters.
- Advanced Materials: Use of thermally stable, wear-resistant, and eco-friendly materials to improve mold lifespan and environmental sustainability.
- Digital Twin Technologies: Simulate mold performance digitally before manufacturing, reducing errors and streamlining modifications.
- Smart Manufacturing: Incorporation of IoT devices for real-time monitoring of machinery, process optimization, and predictive maintenance.
Harnessing these trends positions mold manufacturers as industry innovators capable of delivering exceptional products and services.
Ensuring Sustainability and Environmental Responsibility
Eco-conscious practices are increasingly vital for business reputation and compliance. Leading companies adopt sustainable manufacturing practices such as:
- Recycling and reuse of scrap materials.
- Energy-efficient machinery to reduce carbon footprint.
- Designing molds with eco-friendly materials that facilitate recyclability.
- Implementing LEAN manufacturing principles to eliminate waste and optimize resource use.
By integrating sustainability, mold manufacturers not only contribute to environmental protection but also appeal to a growing base of eco-conscious clients.
Building a Competitive Advantage in the Business of Mold Manufacturing
To outpace competitors and dominate the market, emphasize:
- Customization expertise: Offer bespoke solutions that address specific industry needs.
- Rapid turnaround times: Implement agile manufacturing processes for fast delivery.
- Superior customer support: Provide end-to-end project management, technical assistance, and after-sales service.
- Price competitiveness: Optimize processes to offer reasonable pricing without compromising quality.
- Innovation leadership: Invest in continuous product and process innovation to stay ahead of market trends.
Conclusion: Elevating Your Business as a Leading Mold Manufacturer
The business of mold manufacturing within the metal fabricators industry is ripe with opportunities for innovative, quality-driven companies willing to embrace technology, sustainability, and strategic growth. Success hinges on a steadfast commitment to precision, customer satisfaction, and continuous improvement.
By focusing on these core principles, adopting the latest technological advancements, and building strong industry relationships, your mold manufacturing enterprise can establish a dominant position in this dynamic and highly competitive market. The future of mold manufacturing belongs to those who innovate, adapt, and commit to excellence—qualities that define the most successful businesses in this sector.
For more insights, industry updates, and expert advice, visit deepmould.net, your trusted partner in the metal fabricators industry.