Understanding Plastic Injection Molding: The Future of Manufacturing
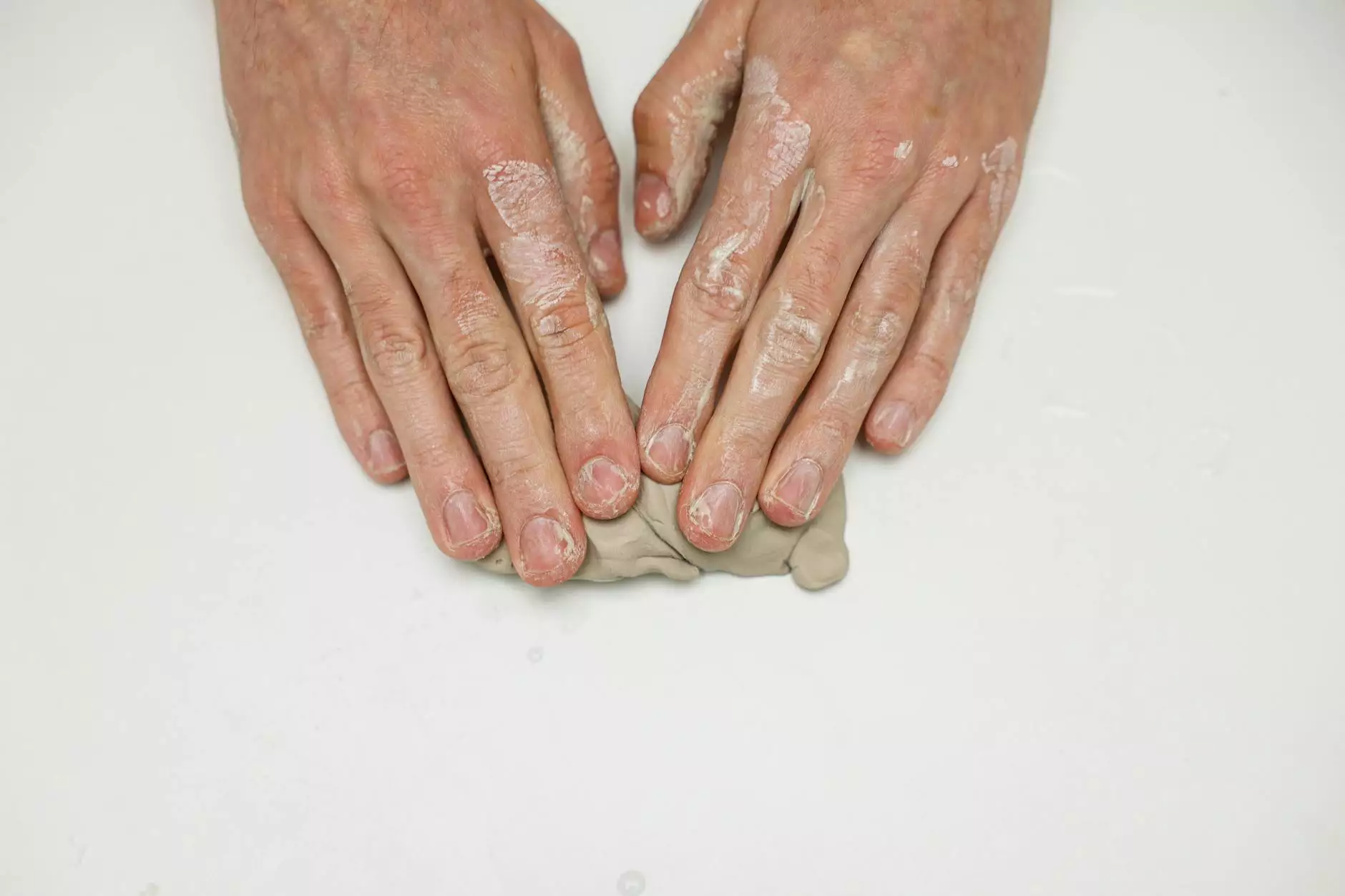
Plastic injection molding is a transformative manufacturing process that has reshaped the landscape of product design and production. This technique allows for the efficient and precise creation of complex plastic parts that are essential in various industries. But what makes plastic injection molding such a powerful tool in modern manufacturing? In this comprehensive article, we will explore the nuances of this process, its myriad applications, and the advantages it offers to businesses looking to innovate and excel.
The Basics of Plastic Injection Molding
At its core, plastic injection molding involves injecting melted plastic into a mold where it cools and solidifies into the desired shape. The process can be broken down into several key stages:
- Material Preparation: The process begins with the selection of appropriate plastic resins, which are often pellets that are heated until they melt.
- Injection: The melted plastic is then injected into a pre-designed mold under high pressure.
- Cooling: After sufficient time in the mold, the plastic cools and hardens, taking on the exact shape of the mold.
- Mold Removal: Once cooled, the mold is opened, and the finished part is ejected.
- Finishing: Additional processes, such as trimming or post-processing, may be applied to the part to achieve the final specifications.
The Advantages of Plastic Injection Molding
There are numerous reasons why plastic injection molding has become a preferred choice for manufacturers, including:
- High Efficiency and Scalability: Once the mold is created, producing large quantities of identical parts is efficient and quick, making it ideal for high-volume manufacturing.
- Cost-Effectiveness: While the initial costs of molds can be significant, the low cost per unit at scale can lead to substantial savings in the long run.
- Design Flexibility: Molds can be designed to create intricate shapes and complex geometries that would be difficult or impossible to achieve with other manufacturing methods.
- Material Variety: A wide range of thermoplastics can be used, allowing for customization based on the specific mechanical and physical properties required.
- Minimal Waste: The process generates very little waste, especially when compared to subtractive manufacturing methods, making it more environmentally friendly.
Applications of Plastic Injection Molding
Plastic injection molding is not confined to a single industry; instead, it spans a multitude of sectors, including:
- Automotive: Used for dashboard components, exterior panels, and interiors due to the lightweight and durable qualities of plastic.
- Consumer Products: Manufacturing everyday items such as packaging, toys, and electronic enclosures.
- Medical Devices: Production of components that require high precision and compliance with safety standards.
- Aerospace: Lightweight and strong plastic parts are commonly used to enhance fuel efficiency and performance.
- Construction: Various fittings and fixtures can be produced, offering prolonged durability and corrosion resistance.
Choosing the Right Plastic Injection Molder
When seeking to harness the benefits of plastic injection molding, selecting the right manufacturer is crucial. Here are some factors to consider:
Expertise and Experience
Look for a company with a strong track record in plastic injection molding, such as DeepMould. Their extensive experience can be vital in ensuring high-quality production.
Advanced Technology
Modern molding machines and technology improve efficiency and precision. Ensure that the provider invests in the latest equipment.
Quality Assurance
Ask about the quality control measures in place. A commitment to quality ensures that your parts meet specifications consistently.
Customer Service
Good communication and support are essential. The right molder will work closely with you throughout the design and production process.
The Future of Plastic Injection Molding
As industries evolve, the demand for more efficient and sustainable practices grows. The plastic injection molding industry is responding with advancements such as:
- Smart Manufacturing: The integration of IoT devices allows for real-time monitoring and optimization of the molding process.
- Sustainable Practices: Innovations in biodegradable materials and recycling processes reduce the environmental impact of plastic usage.
- Automation: Robotics and automation streamline the production process, reducing labor costs and improving accuracy.
- 3D Printing: When used in conjunction with injection molding, 3D printing can speed up prototyping and mold creation.
Conclusion: Embracing the Potential of Plastic Injection Molding
In conclusion, plastic injection molding is more than just a manufacturing technique; it's a vital component in driving innovation and efficiency in various industries. Businesses that leverage this technology can not only improve their production capabilities but also gain a competitive edge in their respective markets.
As the demand for high-quality plastic parts continues to grow, investing in a reliable plastic injection molder like DeepMould will be key to unlocking new opportunities and achieving long-term success. In the ever-evolving landscape of manufacturing, staying informed and adaptable is crucial for any business aiming to thrive.