Plastic Rapid Prototypes Factory: Innovation in Manufacturing
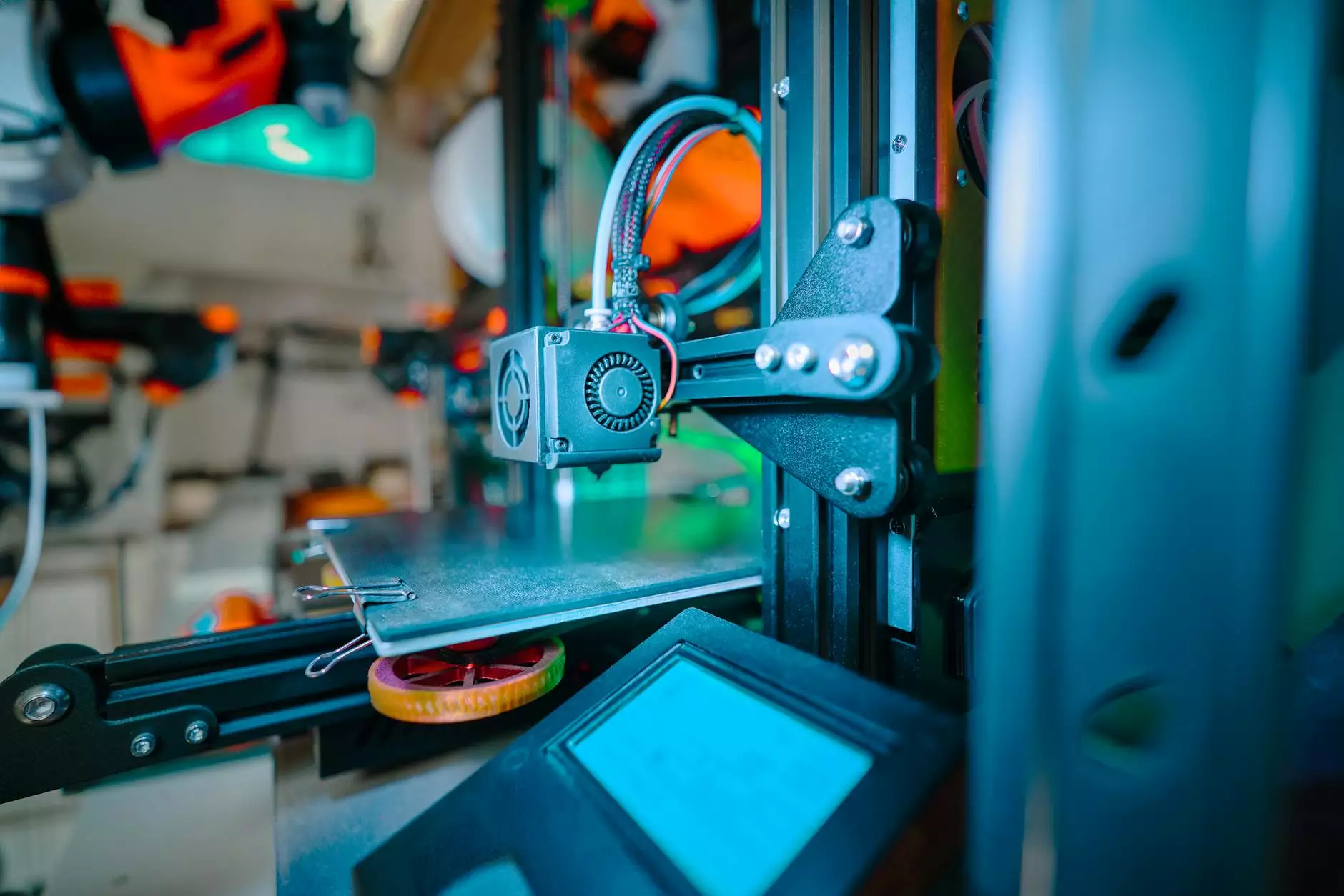
The world of manufacturing is constantly evolving, and at the forefront of this evolution is the plastic rapid prototypes factory. This innovative approach to prototyping not only streamlines the product development process but also enhances the overall quality and efficiency of production. In this article, we will explore the intricacies of plastic rapid prototyping, its benefits, and how it plays a pivotal role in the metal fabrication industry.
Understanding Plastic Rapid Prototyping
Plastic rapid prototyping refers to the process of quickly fabricating a scale model of a physical part or assembly using three-dimensional computer-aided design (CAD) data. The primary goal is to visualize and test the design before committing to production. By harnessing advanced manufacturing technologies, a plastic rapid prototypes factory can produce accurate and functional prototypes that assist in the product development cycle.
The Significance of Rapid Prototyping
In today’s fast-paced market, the ability to transform ideas into tangible products swiftly is crucial. Here are some key reasons why rapid prototyping is significant:
- Speed: Rapid prototyping reduces the time needed to create models, allowing companies to develop and test products faster.
- Cost-Effectiveness: By identifying and resolving design flaws early, rapid prototyping minimizes costs associated with rework and production delays.
- Enhanced Collaboration: Physical prototypes facilitate better communication among stakeholders, fostering collaboration and innovation.
The Process of Rapid Prototyping
In a plastic rapid prototypes factory, the process typically involves the following steps:
- Design Creation: Using CAD software, designers create a digital model of the prototype.
- Material Selection: Factories choose appropriate plastic materials, such as ABS, PLA, or nylon, depending on the specific application and requirements.
- 3D Printing: The selected materials are then subjected to a 3D printing process, which builds the prototype layer by layer.
- Post-Processing: The prototypes may undergo post-processing steps, such as sanding, painting, or assembly, to improve aesthetics and functionality.
- Testing and Iteration: Prototypes are tested for performance, and feedback is used for further refinements.
Advantages of Using a Plastic Rapid Prototypes Factory
The advantages of leveraging a plastic rapid prototypes factory are numerous, and they significantly impact product development:
1. Increased Design Flexibility
Rapid prototyping allows designers to experiment with different shapes, structures, and materials. This flexibility fosters creativity and leads to innovative product solutions that might not have been possible with traditional manufacturing methods.
2. Improved Product Quality
By utilizing prototypes for testing, manufacturers can identify potential issues early in the design process. This proactive approach results in higher-quality final products and increased customer satisfaction.
3. Shortened Time-to-Market
In fiercely competitive markets, being first can provide a significant advantage. Rapid prototyping can dramatically shorten the time it takes to bring a product from concept to market, allowing businesses to seize opportunities faster than their competitors.
4. Customization
Prototyping allows for tailored solutions that meet specific customer needs. Manufacturing custom designs in a plastic rapid prototypes factory makes it easier to adapt to niche markets or individual client demands.
Role of Plastic Rapid Prototyping in Metal Fabrication
Metal fabrication is a robust sector that benefits immensely from the incorporation of rapid prototyping. With a combination of plastic prototypes and metal fabrication, businesses can achieve refined designs, improve fitment, and reduce production time. Here's how:
1. Bridging Design Gaps
Often, metal components require precise fitting with plastic parts. Rapid prototypes serve as a bridge to assess dimensions and coherence between plastic and metal, ensuring that final assemblies fit seamlessly together.
2. Accelerating Tooling Processes
In metal fabrication, creating tooling can be time-consuming and expensive. With prototypes, manufacturers can create and test tooling parameters that enhance production efficiency when working with metals.
3. Testing and Validation
Prototypes allow for extensive testing, ensuring that products operate safely under actual conditions. This critical step is vital for both plastic and metal components, leading to enhanced durability and reliability in final products.
Industries That Benefit from Plastic Rapid Prototyping
The versatility of a plastic rapid prototypes factory enables it to cater to various industries:
- Aerospace: Prototyping aids in developing lightweight components crucial for fuel efficiency.
- Automotive: Rapid prototyping accelerates the design of complex parts while ensuring safety and compliance with regulations.
- Medical: Rapid prototypes are used to create custom surgical tools and implants tailored for patient needs.
- Consumer Goods: Fast-to-market prototypes help businesses respond quickly to changing consumer preferences.
- Electronics: The development of enclosures and components is refined through rapid prototyping, improving functionality and aesthetics.
Best Practices for Engaging with a Plastic Rapid Prototypes Factory
To fully reap the benefits of a plastic rapid prototypes factory, consider the following best practices:
- Clearly Define Your Requirements: Provide specific details about what you need in terms of design, materials, and function.
- Choose the Right Partner: Research potential factories and choose one that specializes in the materials and methods that fit your project.
- Communicate Openly: Keep the lines of communication open to ensure feedback is shared swiftly and effectively.
- Incorporate Feedback: Use the results from prototype testing as critical feedback for design iteratives, refining the product as needed.
- Keep Budget in Mind: While prototyping can save money in the long run, ensure to set a realistic budget and discuss costs upfront with the factory.
Conclusion: The Future of Manufacturing with Plastic Rapid Prototyping
The role of a plastic rapid prototypes factory in modern manufacturing cannot be overstated. As industries continue to evolve, the ability to create prototypes quickly and economically will remain a cornerstone of innovation. By investing in rapid prototyping processes, businesses can not only enhance their design capabilities but also ensure faster time-to-market, improved product quality, and a competitive edge in their respective fields.
At deepmould.net, our commitment to leveraging the latest in rapid prototyping technology ensures that we deliver high-quality solutions tailored to your needs. Whether you are looking to streamline your design processes, reduce costs, or enhance product development cycles, partnering with us guarantees you a pathway to success in an increasingly competitive landscape.
In summary, embracing the power of a plastic rapid prototypes factory is essential for any business intent on innovating and leading in today’s dynamic marketplace.