The Essential Role of **Plastic Injection Mold Tooling Factories** in Modern Manufacturing
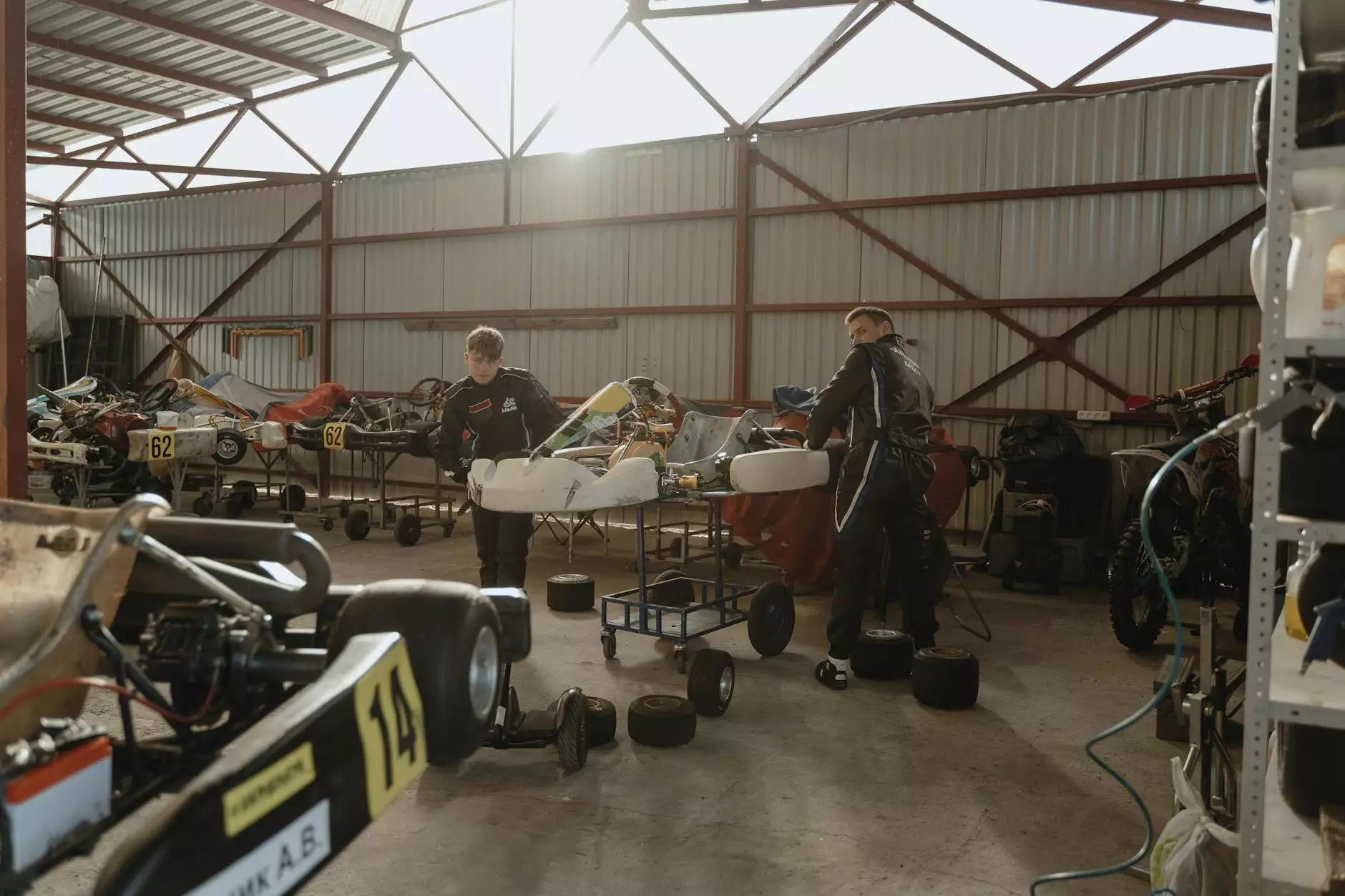
In today's fast-paced manufacturing landscape, the plastic injection mold tooling factory has become a cornerstone of production, revolutionizing the way products are conceived, developed, and delivered to consumers. These factories specialize in creating precise and durable molds used to shape a variety of thermoplastic materials into functional products. In this article, we will delve into the intricacies of plastic injection molding, the technology involved, the benefits it provides, and why partnering with a reputable factory like DeepMould.net is critical for businesses aiming to enhance their manufacturing capabilities.
What is Plastic Injection Molding?
Plastic injection molding is a manufacturing process that involves injecting molten plastic into a pre-formed mold. Once the plastic cools and solidifies, it takes the shape of the mold, resulting in a finished product. This technique is widely used for producing a broad range of items, from household goods to complex automotive components. Its popularity is largely due to its ability to produce high volumes of parts quickly and at a lower cost.
The Process of Plastic Injection Molding
The plastic injection molding process can be broken down into several critical steps:
- Design & Prototyping: The process begins with designing the mold. Engineers and designers use advanced CAD software to create a mold that meets the specifications of the desired product.
- Mold Creation: Once the design is finalized, the mold is manufactured using durable materials like steel or aluminum. This is where a plastic injection mold tooling factory truly excels, as it utilizes precision machining and high-tech equipment to create the molds.
- Injection: The manufacturing process proceeds by heating plastic pellets until they become molten and then injecting this material into the mold under high pressure.
- Cooling: The molded part is allowed to cool and solidify. This cooling step is crucial for ensuring dimensional accuracy.
- Unmolding: After cooling, the mold opens, and the finished part is ejected.
- Finishing: Finally, the part may undergo finishing processes such as trimming, polishing, or surface treatments to meet quality standards.
Advantages of Using a Plastic Injection Mold Tooling Factory
Partnering with a professional plastic injection mold tooling factory like DeepMould.net can offer numerous advantages to businesses across various sectors:
1. Cost-Effectiveness
High-volume production often leads to economies of scale. The initial investment in mold creation can be significant, but when coupled with the high-speed output of plastic injection molding, the cost per unit decreases dramatically.
2. Precision and Consistency
Injection molding allows for the production of highly detailed and precise parts. Molds are engineered to strict specifications, ensuring that every piece produced is virtually identical. This consistency is vital for industries that require a high level of quality and reliability, such as the automotive and aerospace sectors.
3. Versatility of Materials
Plastic injection molding can accommodate a wide variety of thermoplastic materials, including ABS, polypropylene, and polycarbonate. This versatility allows manufacturers to choose the best material suited for their product’s requirements, whether it be strength, flexibility, or heat resistance.
4. Speed of Production
The rapid cycle times associated with injection molding mean that products can be produced much faster than other molding processes. For businesses under pressure to deliver products quickly to market, this speed can provide a significant competitive edge.
5. Reduced Waste
The injection molding process is designed to minimize waste. The molten plastic is injected directly into the mold, and any excess can often be recycled and used for future production runs. This efficiency is key for companies striving to adopt more sustainable practices.
Applications of Plastic Injection Molding
The versatility of plastic injection molding lends itself to a wide range of applications across multiple industries:
- Consumer Products: From toys to kitchenware, many household items are produced using injection molding.
- Automotive Components: Injection-molded parts are used in everything from dashboards to bumpers.
- Medical Devices: Precision is critical in the medical field, and injection molding is perfect for producing sharps, housings, and various tools.
- Electronics: Many electronic housings and components are made via this method, allowing for complex shapes that protect sensitive electronics.
- Industrial Applications: From closures to fittings, many industrial components rely on plastic injection molding technologies.
Choosing the Right Plastic Injection Mold Tooling Factory
Selecting a capable plastic injection mold tooling factory is one of the most critical decisions a business can make. Here are some key factors to consider:
1. Experience and Expertise
Look for a factory with a proven track record in the industry. Experience often equates to expertise in handling complex projects and delivering high-quality products.
2. Technical Capabilities
Assess the factory's technological resources. State-of-the-art machinery and software can dramatically enhance the quality and precision of the molds produced.
3. Customization Ability
Your factory should offer options for customization to cater to your specific product needs, from mold design to material selection.
4. Quality Assurance Processes
Inquire about the quality control measures the factory has in place. Rigorous testing and quality assurance protocols are essential for ensuring product reliability.
5. Customer Service
A responsive and knowledgeable customer service team can facilitate smoother communication and ensure that any concerns are addressed promptly.
The Future of Plastic Injection Molding
The plastic injection mold tooling factory sector is continually evolving with advancements in technology. Innovations such as 3D printing for mold making, the use of smart manufacturing techniques, and advancements in material science are all shaping the future of this industry. As sustainability becomes increasingly important, the development of bio-based plastics and recycling technologies will also likely influence the design and operations of injection molding factories.
Conclusion
In conclusion, the importance of plastic injection mold tooling factories in modern manufacturing cannot be overstated. Their ability to produce high-quality, consistent, and cost-effective products makes them indispensable across various industries. By partnering with a leading factory like DeepMould.net, businesses can not only enhance their production capabilities but also position themselves for future growth in an ever-competitive marketplace. Investing in top-notch tooling and manufacturing processes is vital for any business looking to thrive in today’s economy.
Contact Us
For more information about our services and how we can assist you in your manufacturing needs, visit DeepMould.net or contact us today.